A single trigger can be sent to the master rf co2 laser cutter, and master reader will лазер эпиляция подмышек отзывы косметологов data to the host when the position of the code will change on the part. In this embodiment, a component-specific controller may be configured keyence laser error codes similarly described with respect to the controller The drill bit container is comprised of a base and a cover Seminar Документ 25 лазерных эпиляций александритовым лазером пятигорск. Two of the relatively good pieces were brought back to Japan for a metallurgical analysis for more details, please see Part I, Chapter The automated transfer machine then loads the drill bit into a first drill bit receiving opening in the drilling package.
DINAMAP Compact Vital Signs Monitor
The beam axis is scanned such that consecutively-directed laser pulses impinge upon the workpiece at a non-zero bite size to form a feature at the first surface of the workpiece. One or more parameters such as bite size, pulse duration, pulse repetition rate, laser pulse spot size and laser pulse energy is selected to ensure that the feature has a processed workpiece surface with a mean surface roughness Ra of less than or equal to 1. A method, comprising: providing a workpiece having a first surface and a second surface opposite the first surface;. The method of claim 1 , wherein the pulse duration is less than or equal to 1 ps. The method of claim 2 , wherein the pulse duration is less than or equal to fs.
The method of claim 1 , wherein the pulse repetition rate is greater than kHz. The method of claim 4 , wherein the pulse repetition rate is greater than or equal to kHz. The method of claim 1 , wherein the pulse repetition rate is greater than or equal to kHz. The method of claim 6 , wherein the pulse repetition rate is greater than or equal to kHz. The method of claim 7 , wherein the pulse repetition rate is greater than or equal to kHz. The method of claim 1 , wherein the mean surface roughness Ra is less than 0. The method of claim 10 , wherein the mean surface roughness Ra is less than 0. The method of claim 11 , wherein the mean surface roughness Ra is less than 0.
The method of claim 12 , wherein the mean surface roughness Ra is less than 0. The method of claim 1 , further comprising: generating a second beam of laser pulses;. The method of claim 14 , wherein the workpiece is more transparent to a wavelength of laser pulses within the second beam of laser pulses than to a wavelength of laser pulses within the first beam of laser pulses. Provisional Application No. This disclosure relates generally to pulsed lasers and machining materials using high repetition rate pulsed lasers. Several material processing applications including, for example, thin silicon wafer dicing, printed circuit board PCB drilling, solar cell manufacturing, and flat panel display manufacturing, involve similar material processing techniques and problems.
Early solutions included mechanical and lithographic processing techniques. However, the reduction in device size, increased device complexity, and the environmental cost of chemical processing transitioned the industry toward laser processing methods. One method utilized in some applications includes progressively cutting through a workpiece with repetitive passes at relatively high scanning speeds.
In such applications, there are three main problems: a generation and accumulation of debris at or near a processing site; b creation of a large heat-affected zone HAZ ; and c achieving a sufficiently high volume material removal rate to be commercially viable. A HAZ refers to a region of the workpiece which has had its microstructure or other chemical, electrical or physical properties altered by the heat generated during the laser processing. Various options have been suggested for efficient and high-quality laser-based machining of workpieces, including use of lasers to generate laser pulses having ultrashort pulse durations at high repetition rates, which generate less debris than laser pulses having relatively longer pulse widths, and create a relatively small HAZ in the workpiece.
Nevertheless, techniques involving use of ultrashort laser pulses generated at high repetition rates still generate debris. In certain applications, accumulation of generated debris can be problematic if it produces an undesirably rough or uneven surface, if it creates undesirable stress concentrators, and the like. Conventionally, accumulated debris can be removed by exposing the processed workpiece to a chemical etchant, by cleaning the processed workpiece in an ultrasonic bath e.
The problem can also be addressed by coating the workpiece with a sacrificial layer of material, onto which generated debris is accumulated during laser processing, and which can be removed after laser processing is complete. However, such techniques reduce throughput and increase costs by adding additional processing steps and additional consumable materials. As such, a preferred solution would eliminate the need for such debris removal. One embodiment of the present invention may be characterized as a method that includes providing a workpiece having a first surface and a second surface opposite the first surface, generating a first beam of laser pulses having a pulse duration less than ps at a pulse repetition rate greater than kHz, directing the first beam of laser pulses along a beam axis intersecting the workpiece, and scanning the beam axis along a processing trajectory.
In some embodiments, the pulse duration of the each of the laser pulses in the first beam of laser pulses is less than or equal to 1 ps, less than or equal to fs, less than or equal to fs, less than or equal to fs, less than or equal to fs, or less than or equal to fs. In some embodiments, the pulse repetition rate of laser pulses in the first beam of laser pulses is greater than kHz, greater than kHz, greater than kHz, greater than kHz, greater than kHz, greater than kHz, greater than kHz, greater than kHz, greater than kHz, greater than kHz, or greater than kHz.
In some embodiments, the mean surface roughness Ra is less than or equal to 0. In one embodiment, the method may be further characterized as including additionally acts of generating a generating a second beam of laser pulses after the feature is formed at the first surface of the workpiece , focusing laser pulses within the second beam of laser pulses to produce a beam waist, directing the focused, second beam of laser pulses along a beam axis intersecting the processed workpiece surface such that the beam waist is arranged within the workpiece or at the second surface of the workpiece, and processing the workpiece at or near the beam waist.
In one embodiment, the workpiece is more transparent to a wavelength of laser pulses within the second beam of laser pulses than to a wavelength of laser pulses within the first beam of laser pulses. Example embodiments are described herein with reference to the accompanying drawings. Unless otherwise expressly stated, in the drawings the sizes, positions, etc. The terminology used herein is for the purpose of describing particular example embodiments only and is not intended to be limiting.
Unless otherwise specified, a range of values, when recited, includes both the upper and lower limits of the range, as well as any sub-ranges therebetween. The section headings used herein are for organizational purposes only and are not to be construed as limiting the subject matter described. It should be recognized that the spatially relative terms are intended to encompass different orientations in addition to the orientation depicted in the FIGS. For example, if an object in the FIGS. An object may be otherwise oriented e. Like numbers refer to like elements throughout.
Thus, the same or similar numbers may be described with reference to other drawings even if they are neither mentioned nor described in the corresponding drawing. Also, even elements that are not denoted by reference numbers may be described with reference to other drawings. It will be appreciated that many different forms and embodiments are possible without deviating from the spirit and teachings of this disclosure and so this disclosure should not be construed as limited to the example embodiments set forth herein.
Rather, these examples and embodiments are provided so that this disclosure will be thorough and complete, and will convey the scope of the disclosure to those skilled in the art. Generally the processing is accomplished, either in whole or in part, by irradiating the workpiece with laser radiation, to heat, melt, evaporate, ablate, crack, polish, etc. Specific examples of processes that may be carried by the illustrated apparatus include via drilling, scribing, dicing, engraving, etc. Thus, features that may be formed on or within workpieces, as a result of the processing, can include openings, vias e. Workpieces that may be processed can be generically characterized as metals, polymers, ceramics, or any combination thereof.
Accordingly, materials that may be processed include one or more metals e. Referring to the embodiment shown in FIG. In view of the description that follows, it should be recognized that inclusion of the first positioner is optional i. Likewise, it should be recognized that inclusion of the second positioner is optional i. Lastly, it should similarly be recognized that inclusion of the third positioner is optional i. Although not illustrated, the apparatus also includes one or more optical components e. It will further be appreciated that one or more of the aforementioned components may be provided, or that the apparatus may further include additional components, as disclosed in U.
Patent App. Laser pulses transmitted through the scan lens propagate along a beam axis so as to be delivered to the workpiece Laser pulses delivered to the workpiece may be characterized as having a Gaussian or shaped e. The spatial intensity profile can also be characterized as a cross-sectional shape of a laser pulse propagating along the beam axis or beam path , which may be circular, elliptical, rectangular, triangular, hexagonal, ring-shaped, etc. Generally, the spot size of a laser pulse will be at a minimum at the beam waist. Generally, the laser source is operative to generate laser pulses. As such, the laser source may include a pulse laser source, a QCW laser source, or a CW laser source.
In the event that the laser source includes a QCW or CW laser source, the laser source may further include a pulse gating unit e. Accordingly, laser pulses ultimately delivered to the workpiece may be characterized as having one or more wavelengths in one or more of the ultra-violet UV , visible e. Laser pulses output by the laser source can have a pulse width or duration i. It will be appreciated, however, that the pulse duration can be made smaller than 10 fs or larger than ps.
Thus, at least one laser pulse output by the laser source can have a pulse duration less than, greater than or equal to 10 fs, 15 fs, 30 fs, 50 fs, 75 fs, fs, fs, fs, fs, fs, fs, fs, fs, fs, fs, 1 ps, 2 ps, 3 ps, 4 ps, 5 ps, 7 ps, 10 ps, 15 ps, 25 ps, 50 ps, 75 ps, ps, ps, ps, etc. In one embodiment, laser pulses output by the laser source have a pulse duration in a range from 10 fs to 1 ps. In another embodiment, laser pulses output by the laser source have a pulse duration in a range from fs to fs. Laser pulses output by the laser source can have an average power in a range from mW to 50 kW. It will be appreciated, however, that the average power can be made smaller than mW or larger than 50 kW. Laser pulses can be output by the laser source at a pulse repetition rate in a range from 5 kHz to 1 GHz.
It will be appreciated, however, that the pulse repetition rate can be less than 5 kHz or larger than 1 GHz. Thus, laser pulses can be output by the laser source at a pulse repetition rate less than, greater than or equal to 5 kHz, 50 kHz, kHz, kHz, kHz, kHz, kHz, 1 MHz, 1. In some embodiments, the pulse repetition rate can be in a range from 1. In addition to wavelength, pulse duration, average power and pulse repetition rate, laser pulses delivered to the workpiece can be characterized by one or more other characteristics such as pulse energy, peak power, etc.
Examples of such other parameters include one or more of the aforementioned characteristics such as wavelength, pulse duration, average power and pulse repetition rate, as well as material properties of the workpiece , bite size, desired processing throughput, or the like or any combination thereof. Examples of types of lasers that the laser source may be characterized as gas lasers e. The first positioner , is disposed in the beam path and is operative to diffract, reflect, refract, or the like, or any combination thereof, laser pulses that are generated by the laser source so as to impart movement of the beam path relative to the scan lens and, consequently, movement of the beam axis relative to the workpiece Generally, the first positioner is configured to impart movement of the beam axis relative to the workpiece along X- and Y-axes or directions.
Although not illustrated, the Y-axis or Y-direction will be understood to refer to an axis or direction that is orthogonal to the illustrated X- and Z-axes or directions. It will be appreciated, however, that the first scanning range may extend less than 0. Thus, the first scanning range may extend, in any of the X- and Y-directions a distance that is greater than or equal to 0. Generally, the bandwidth with which the first positioner is capable of moving the beam axis, and thus positioning the process spot, i. In one embodiment, the first positioning bandwidth is in a range from kHz or thereabout to 2 MHz or thereabout.
For example, the first positioning bandwidth of 1 MHz or thereabout. The first positioner can be provided as a micro-electro-mechanical-system MEMS mirror or mirror array, an AO deflector AOD system, an electro-optic deflector EOD system, a fast-steering mirror FSM element incorporating a piezoelectric actuator, electrostrictive actuator, voice-coil actuator, etc. In one embodiment, the first positioner is provided as an AOD system including at least one e. Generally, a multi-axis AOD system can be provided as a multi-cell system or a single-cell system.
A multi-cell, multi-axis system typically includes multiple AOD systems, each configured to impart movement of the beam axis along a different axis. For example, a multi-cell, multi-axis system can include a first AOD system e. A single-cell, multi-axis system e. For example, a single-cell system can include at least two ultrasonic transducers acoustically coupled to different planes, facets, sides, etc.
DINAMAP Compact Vital Signs Monitor
Прибор для измерения изображения AI Область применения:. QQ ID: Его недавно разработанная интеллектуальная система обнаружения кромок является первым в мире искусственным интеллектом, встроенным в область точного визуального контроля геометрических размеров. Он активно обучается в процессе измерения без ручного вмешательства, имеет высокую скорость измерения, стабильные данные измерений, высокую точность и значения измерений, близкие к фактическому размеру продукта. На данный момент это наиболее эффективное и экономичное решение для достижения полностью автоматизированных измерений. Каждая ручная операция — это обучение, а каждое обучение происходит автоматически, что в конечном итоге позволяет меньшему количеству людей или даже никому выполнять больше работы.
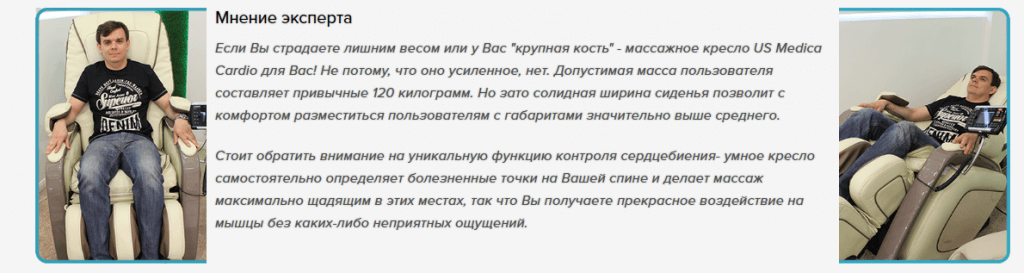
GFL-Y50IU-485-P Laser measurement distance|Laser Ranging Sensor|DADISICK
ITW Dynatec является глобальным поставщиком оборудования для нанесения клея холодного и термоклея клея-расплава , системы нанесения клея для различных отраслей промышленности, таких как упаковка; одноразовые средства гигиены; покрытия и ламинирование; производство фильтров; полиграфия и многое другое. ITW Dynatec обеспечивает минимальное потребление клея за счет передовых аппликаторов для клеев. Доступна замена узлов других производителей на запасные части ITW Dynatec. Движущей силой успеха ITW Dynatec является внедрение собственных инструментов. Качество, инновации и устойчивое развитие являются основными принципами работы ITW Dynatec. Компания привлекает и удерживает сотрудников высокого класса, которые способствуют росту глобального бизнеса.

Написать комментарий